In the world of tablet manufacturing, multi-station rotary presses stand out as vital equipment for large-scale production. These machines are engineered to produce tablets efficiently and uniformly, making them a staple in pharmaceutical, nutraceutical, and chemical industries. With the capacity to produce thousands of tablets per hour, multi-station rotary presses are essential for meeting the high demands of modern production.
This guide will delve into the workings, benefits, and applications of multi-station rotary presses, as well as address common questions about their operation and maintenance.
What is a Multi-Station Rotary Press?
A multi-station rotary press is a high-speed tablet compression machine that uses multiple sets of punches and dies arranged on a rotating turret. This setup allows for the simultaneous production of multiple tablets, greatly enhancing efficiency and output. By compressing powders or granules into uniform tablets, these machines ensure consistency in size, weight, and hardness, which is critical in pharmaceutical manufacturing.
How Does a Multi-Station Rotary Press Work?
The operation of a multi-station rotary press can be broken down into several key stages:
- Powder Feeding: The powder or granule mixture is loaded into a hopper, which distributes the material evenly into the die cavities.
- Die Filling: The rotating turret brings each die under the feed frame, where it is filled with a precise amount of powder. The uniform filling process ensures that each tablet has consistent weight and composition.
- Compression: The punches compress the powder within the die cavities as the turret rotates. The upper and lower punches apply pressure simultaneously to form solid tablets, with the compression force adjustable based on tablet requirements.
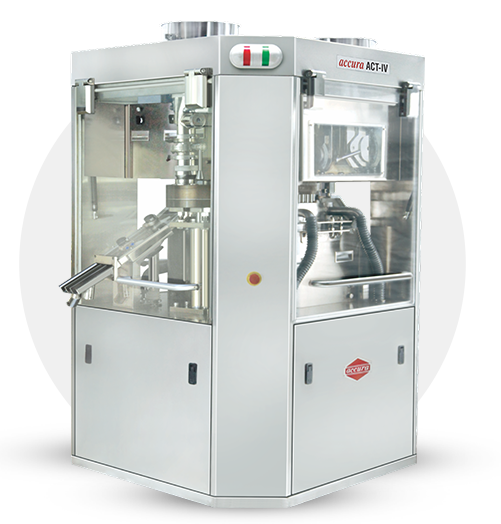
- Ejection: The finished tablets are ejected from the dies and collected, ready for further processing or packaging. This continuous rotation allows for the high-speed production of tablets.
Key Features of High-Speed Multi-Station Rotary Presses
- High Throughput: A multi-station rotary press can produce thousands of tablets per hour, making it ideal for large-scale production.
- Adjustable Compression Force: The ability to fine-tune the compression force ensures that each tablet meets the desired hardness and thickness specifications.
- Automated Controls: Many modern presses come with advanced automation, such as programmable logic controllers (PLC), touch-screen interfaces, and real-time monitoring to maintain precision and quality.
- Multi-Punch Design: The use of multiple sets of punches and dies on a rotating turret increases productivity and ensures consistent tablet quality.
- Compact and Space-Efficient: Despite their high output, many multi-station rotary presses have a compact design, making them suitable for facilities with limited space.
Benefits of Using a Multi-Station Rotary Press
- Efficiency and Speed: The ability to produce multiple tablets simultaneously greatly enhances production speed and reduces manufacturing time.
- Uniform Quality: Automated systems ensure that each tablet has consistent weight, size, and hardness, which is crucial for pharmaceutical and nutraceutical compliance.
- Cost-Effective Production: The high output of these machines reduces labor costs and minimizes material waste.
- Flexibility: By changing the punch and die sets, a multi-station rotary press can produce tablets in various shapes and sizes, making it versatile for different formulations.
- User-Friendly Operation: Modern presses are designed with intuitive interfaces, making them easy to operate and monitor.
Applications of Multi-Station Rotary Presses
- Pharmaceutical Industry: The primary use of these machines is in pharmaceutical manufacturing, where they compress active ingredients and excipients into uniform medicinal tablets.
- Nutraceutical Industry: High-speed multi-station rotary presses are used to produce vitamins, minerals, and dietary supplements in tablet form.
- Chemical Industry: These presses are used for compressing various chemicals into tablets for industrial applications.
- Food Industry: They can also be used to create tablets for candies and other food supplements.