Tablet press machines, also known as tablet compression machines or tableting machines, are integral to the pharmaceutical, nutraceutical and chemical industries. These machines compress powders or granules into tablets of uniform size, weight and hardness. With the rise of modern tablet press machines, such as fully computerized tablet press machines and high-speed rotary tablet press machines, ensuring safety during operation is paramount to protect both operators and equipment. This article explores key safety measures to follow when operating tablet press machines.
Understanding Tablet Press Machines
A tablet press machine works by compressing powder between two punches (upper and lower) within a die. These machines range from semi-automatic to fully automatic tablet press machines, with advanced options like single rotary tablet press machines and double rotary tablet press machines. While these machines boost efficiency and precision, adhering to proper safety protocols is essential to maintain smooth operations and prevent accidents.
Training and Operator Knowledge
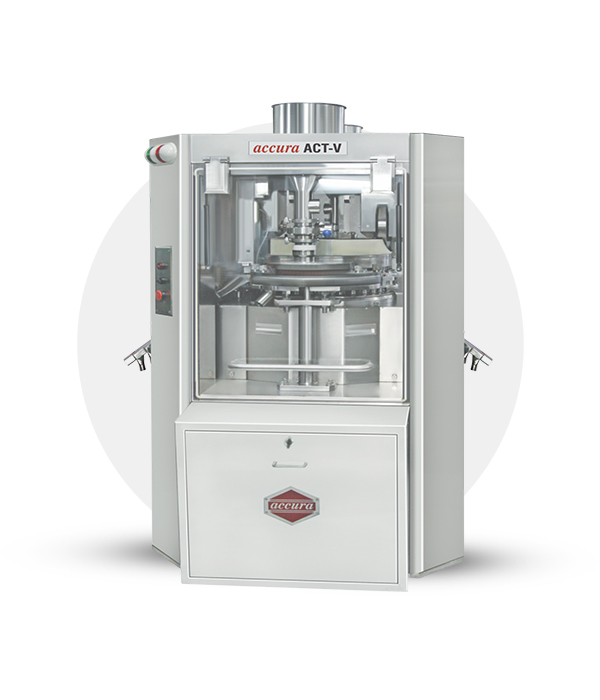
Why Training Is Essential?
Operators must be well-trained in using the tablet press machine to minimize risks. Training includes understanding the machine’s components, functionality and safety protocols.
Best Practices:
- Conduct hands-on training for all operators to familiarize them with the machine’s mechanisms.
- Focus on critical components like the die, punches, feeders and advanced features of computerized models.
- Regularly organize refresher courses to keep operators updated on operational safety and new technologies.
Pre-Operation Inspections
Importance of Pre-Checks
Performing thorough inspections before starting the machine helps identify potential issues that could cause malfunctions or accidents.
Checklist for Pre-Operation Inspections:
- Ensure all components, including the hopper, punches and dies, are clean and free from residues.
- Inspect punches and dies for wear, cracks or other damages that could compromise output quality.
- Confirm proper alignment and lubrication of moving parts to avoid unnecessary strain or overheating.
Proper Handling of Raw Materials
Avoiding Contamination
Powders and granules used in tablet compression must be handled with care to avoid contamination or clumping, which can lead to machine blockages.
Safety Tips:
- Store raw materials in sealed, clean and designated storage areas to avoid exposure to contaminants.
- Operators must wear gloves, masks and aprons when handling materials to prevent contamination.
- Use only tested and approved materials compatible with the machine’s specifications.
Wearing Personal Protective Equipmentn
Essential PPE for Operators
Operators should always wear appropriate PPE to protect themselves from dust, noise and accidental injuries.
Standard PPE Includes:
- Safety goggles: Protect eyes from dust and fine particles.
- Gloves: Prevent direct contact with chemicals and reduce risks of cuts or burns.
- Dust masks: Minimize inhalation of fine powders during operations.
- Ear protection: Essential when working with high-speed machines that generate significant noise levels.
Following Manufacturer Guidelines
Adherence to Specifications
Each tablet press machine has unique features and operational requirements. Following the manufacturer’s manual ensures optimal performance and safety.
Key Recommendations:
- Operate within the speed and pressure limits specified in the manual.
- Use only recommended tooling, dies and compatible components.
- Avoid unauthorized modifications to machine parts to prevent performance issues and ensure compliance.
Ensuring Machine Maintenance
Regular Maintenance Routines
Proper maintenance prevents mechanical failures and extends the lifespan of the tablet press machine.
Maintenance Best Practices:
- Clean the machine after every use to remove powder residues that can clog parts.
- Inspect and replace worn punches, dies and other components promptly.
- Schedule periodic servicing by qualified technicians, particularly for advanced models like fully automatic machines.
Emergency Preparednesss
Preparedness for Unexpected Issues
Operators should be trained to handle emergencies such as power outages, material blockages or overheating.
Emergency Measures Include:
- Train operators to activate the emergency stop function in critical situations.
- Keep fire extinguishers and first-aid kits readily accessible near the machine.
- Establish clear response plans for power outages, overheating and other emergencies.
Dust Management and Ventilation
Control of Dust Generation
Dust is a common byproduct of tablet compression, particularly in high-speed machines like the high-speed double rotary tablet press machine. Uncontrolled dust can pose health risks and lead to machine malfunctions.
Dust Control Measures:
- Install high-quality dust extraction systems around the machine.
- Use enclosed systems to reduce airborne particles during operations.
- Regularly clean the environment to prevent dust buildup.
Avoiding Overloading
Impact of Overloading
Overloading a tablet press machine with excessive powder can strain the machine, causing wear and potential breakdowns.
Precautions:
Follow the manufacturer’s guidelines for hopper loading capacities. Monitor performance for signs of overloading, such as abnormal noises or slowed operations.Monitoring Compression Pressure
Importance of Accurate Pressure Settings
Excessive or inadequate compression pressure can affect tablet quality and damage machine components.
Steps for Pressure Control:
- Adjust pressure based on tablet size and the properties of the raw material.
- Regularly calibrate the machine to ensure precise pressure readings.
- Leverage pressure-monitoring features in advanced computerized machines for real-time adjustments.
Avoiding Manual Interference During Operation
Preventing Injuries
Manual interference while the machine is running can lead to severe accidents, such as crushed fingers or entanglement.
Guidelines:
- Never attempt to adjust or clean parts while the machine is operational.
- Use appropriate tools for adjustments instead of bare hands.
- Ensure all safety guards and covers are in place before starting the machine.
Handling Lubricants and Cleaning Agents
Safe Use of Chemicals
Lubricants and cleaning agents are essential for maintaining machine performance but must be handled carefully to avoid accidents or contamination.
Safety Tips:
- Use FDA-approved, non-toxic lubricants for machine parts.
- Store cleaning agents away from the production area to avoid accidental spills.
- Follow proper disposal methods for chemical waste to ensure environmental safety.
Implementing Automation Safeguards
Advantages of Automation
Advanced tablet press machines, such as fully automatic tablet press machines, equipped with safety features that minimize risks.
Automation Features to Leverage:
- Overload protection systems to prevent excessive pressure.
- Automatic shutdown mechanisms in case of malfunctions or overheating.
- Real-time monitoring for pressure, speed and temperature to detect irregularities early.