Tablet compression machines, also known as tablet presses, are integral to the pharmaceutical industry, ensuring tablets of uniform size, weight and shape. With the diversity of machine types and the increasing demand for complex tablet formulations, selecting the right compression machine requires careful consideration. This article will guide you through the critical factors to consider when choosing a tablet compression machine tailored to your pharmaceutical needs.
What is Tablet Compression Machines?
Tablet compression machines are used to compress powder or granules into tablets. These machines operate through precise mechanisms involving key components such as the hopper, die, punches and turret. Different types of machines, from single rotary presses to bilayer and multi-layer machines, cater to various production requirements.
To ensure optimal performance and cost-effectiveness, it’s essential to select a machine that aligns with your production goals, tablet design and industry compliance standards.
Key Considerations for Selecting the Right Compression Machine
Choosing the right machine involves understanding your specific production requirements, regulatory constraints and operational needs. Below are the critical factors to consider:
Type of Tablets to Be Produced
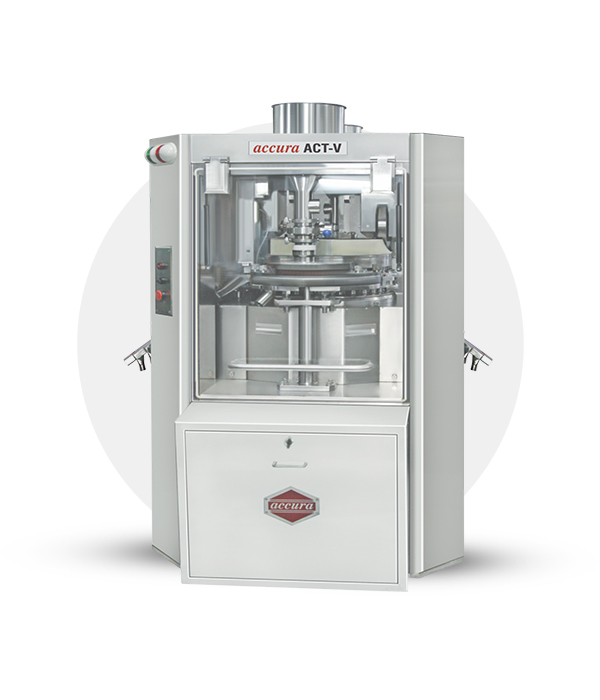
Single-Layer Tablets
If your focus is on producing simple formulations with a single active ingredient, a single rotary tablet press machine may suffice. These machines are cost-effective and efficient for standard applications.
Bilayer or Multi-Layer Tablets
For more advanced formulations, such as bilayer tablets, a bilayer compression machine is essential. These machines allow for combining two or more active ingredients in separate layers, enabling modified-release formulations or combination therapies.
Effervescent and Coated Tablets
If producing coated or effervescent tablets, ensure the machine supports customization options like multi-layer compression or high-pressure capabilities.
Production Volume
Small-Scale Production
For small or pilot-scale production, a manual or semi-automatic tablet press is suitable. These machines are cost-effective and ideal for producing small batches.
Large-Scale Manufacturing
For high-volume production, a high-speed rotary tablet press machine is recommended. These machines have multiple tooling stations, enabling the production of thousands of tablets per hour while maintaining uniformity.
Regulatory Compliance
Pharmaceutical manufacturing must adhere to strict regulatory standards, such as 21 CFR compliance. When selecting a tablet compression machine:
- Ensure it meets Good Manufacturing Practices.
- Opt for machines with built-in data recording and monitoring systems for quality assurance.
- Look for compliance with pharmaceutical validation requirements to avoid production setbacks.
Tablet Size and Shape
Customization Options
Consider the size, shape and branding of your tablets. Machines with versatile tooling capabilities, such as multi-tool turrets, allow manufacturers to produce tablets in various shapes and sizes.
Embossing and Branding
If branding or embossing is required, ensure the machine supports customized punches and dies for your tablet designs.
Compression Force and Precision
Compression force determines the hardness and structural integrity of the tablets. Machines with:
- Adjustable compression rollers offer flexibility for different tablet formulations.
- Real-time monitoring systems ensure consistent compression, critical for maintaining uniform weight, size and shape.
Automation and Advanced Features
Modern tablet presses come with automation features that enhance productivity and accuracy. When selecting a machine:
- Look for fully computerized tablet press machines with automated controls for precise filling, compression and ejection.
- Consider machines with real-time monitoring for weight, thickness and hardness.
- Opt for features like overload protection to prevent machine damage during production.
Dust Management and Safety Features
Dust Control
Tablet compression generates dust, which can affect machine performance and operator safety. Machines with integrated dust extraction systems and sealed compression zones ensure a clean and safe working environment.
Safety Mechanisms
Choose machines equipped with:
- Emergency stop buttons and Protective guards over moving parts.
- Alarms for overheating or pressure overload.
Ease of Maintenance and Cleaning
Machines with a modular design and easily removable parts simplify maintenance and reduce downtime. Additionally:
- Ensure the machine is made of corrosion-resistant materials like stainless steel to meet hygiene standards.
- Look for machines with tool-free disassembly for faster cleaning and reassemble the tools properly for easy maintenance.
Budget and Long-Term Costs
While initial cost is a significant factor, consider the total cost of ownership, including:
- Maintenance and servicing costs and surfacing the replacement expenses.
- Energy consumption and efficiency.
Investing in a high-quality machine with advanced features might have higher upfront costs but can save money in the long run through enhanced productivity and lower downtime.
Tips for Selecting the Right Compression Machine
- Define Your Requirements: Understand your production needs, tablet formulations and target audience before selecting a machine.
- Focus on Scalability: Choose a machine that can grow with your business and accommodate future demands.
- Prioritize Quality Control: Look for machines with built-in monitoring systems to maintain tablet consistency and quality.
- Evaluate Space Constraints: Ensure the machine fits within your facility layout while allowing room for cleaning and maintenance.
- Test Before Purchase: Conduct trials with sample formulations to ensure the machine meets your specific requirements.
Why Choosing the Right Compression Machine Matters?
The right tablet compression machine can significantly impact your production efficiency, product quality and compliance with regulatory standards. By carefully evaluating your needs and aligning them with the machine’s capabilities, you can ensure smooth operations, reduced costs and consistent tablet production.