Uniformity in tablet size and weight is one of the most critical quality parameters in pharmaceutical manufacturing. Variations can affect active ingredient dosage, tablet dissolution, stability and compliance with pharmaceutical standards. The foundation of this consistency lies in the precise operation and setup of a tablet press machine.
Modern equipment, whether it's a compact single punch press or a high-capacity rotary tablet press, is designed to minimize variability and maximize control over key parameters. By understanding how these machines function and how to configure them properly, manufacturers can achieve consistent tablet characteristics from batch to batch.
This guide outlines the key technical practices, machine settings and process controls that help ensure tablet uniformity in real-world production environments.
Fundamentals of Tablet Compression and Uniformity
Tablet presses work by compressing a measured volume of powder within a die using upper and lower punches. The uniformity of each tablet’s weight and dimensions depends on several tightly controlled factors.
Key Technical Factors:
- Die fill volume - Determines the tablet’s weight.
- Compression force - Affects the tablet’s hardness and thickness.
- Dwell time - Influences tablet integrity during pressing.
- Powder flow properties - Directly impact fill consistency.
To minimize weight and size variability, equipment should have precision-engineered cams, fill systems and force sensors to monitor and adjust each compression cycle.
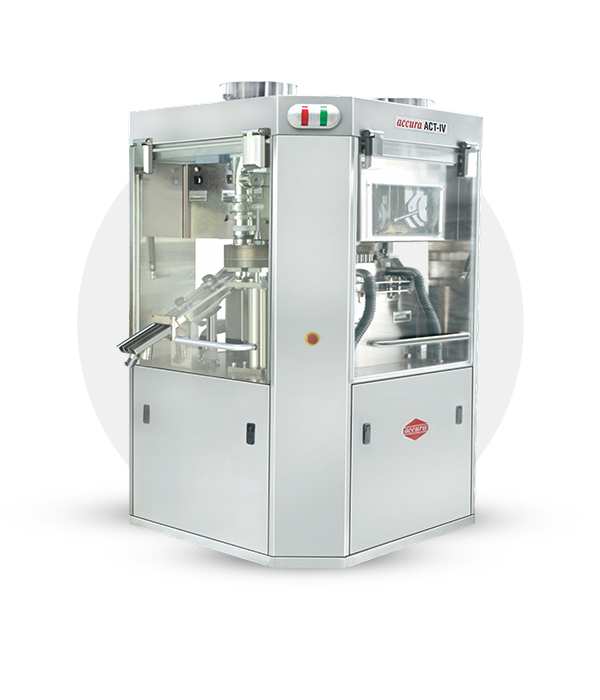
Choosing the Right Press for Operational Needs
Not all equipment is created equal. The choice of tablet press machines must align with production scale, formulation behavior and quality requirements.
Single Punch Press Machines:
These are preferred for small batches or development work. While simpler, they allow fine-tuning of compression parameters and are effective for trials or personalized medicine manufacturing.
Rotary Press Machines:
Suited for high-volume production, rotary systems feature multiple stations that compress tablets in a continuous cycle. These machines offer superior repeatability due to consistent fill mechanisms and pressure control systems. Integration with in-line weight checks and feedback loops enhances overall consistency.
Optimizing Machine Setup for Uniform Output
Achieving uniform tablets is not only about machine selection-it also depends on proper calibration and setup.
Best Practices for Setup:
- Calibrate fill cams to control powder volume entering the die cavity.
- Verify punch alignment to ensure symmetrical compression.
- Adjust pre-compression force to eliminate trapped air in powders.
- Use high-quality tooling to maintain dimensional accuracy.
Technicians should regularly inspect the condition of punches and dies, as worn tooling can result in inconsistent weights or thickness.
Managing Powder Flow and Granulation Quality
Powder flow characteristics directly influence tablet weight. Irregular or poor-flowing granules can lead to inconsistent die filling, especially in high-speed presses.
Tips for Improved Powder Flow:
- Use uniformly sized granules with low moisture content.
- Incorporate glidants or lubricants where needed.
- Maintain stable hopper feed with constant agitation or feeders.
Granulation that flows well ensures better control during the die fill phase, especially on rotary tablet press machines, where speed can amplify variability.
Monitoring and Controlling Compression Parameters
Real-time monitoring is key to controlling quality during compression. Advanced machines now include sensors and software for detecting anomalies mid-production.
Parameters to Monitor:
- Tablet weight deviation
- Compression force variations
- Punch penetration depth
- Tablet thickness and hardness
By linking tablet weight feedback with automatic press adjustments, operators can maintain consistent production quality without constant manual checks.
Preventive Maintenance and Calibration
Uniformity isn't just a result of good setup-it also relies on machine health. Regular maintenance and calibration are essential for reliable operation.
Routine Checks Include:
- Tooling inspection and polishing
- Force transducer calibration
- Lubrication of mechanical parts
- Software and control system updates
A well-maintained tablet press delivers predictable performance, ensuring minimal fluctuation in compression outcomes.
Ensuring Operator Training and Process Documentation
The skill of the operator is just as important as the machine itself. Properly trained personnel understand how to detect process drift and respond appropriately.
Key Operator Responsibilities:
- Accurate batch recordkeeping
- Routine in-process checks
- Immediate adjustment of fill depth or pressure if needed
- Understanding of equipment controls and alarms
A culture of accountability, backed by SOPs, reduces the chance of unnoticed inconsistencies, leading to more reliable tablet production.