Tablet compression is a fundamental process in pharmaceutical manufacturing, but it also presents a major operational challenge: dust. Every compression cycle release fine powder that can accumulate in machines, contaminate clean zones and pose inhalation hazards. Left unmanaged, this airborne particulate interferes with production efficiency and equipment reliability.
The integration of dedicated dust extraction technology into the tablet compression process addresses these issues head-on. Using a high-performance dust extractor ensures a cleaner working environment, protects sensitive components and enhances the overall reliability of the production line. For manufacturers seeking operational stability and regulatory compliance, dust management systems are now essential-not optional.
Dust Generation in Tablet Compression
During tablet formation, material movement and mechanical interaction between powders and punches produce residual airborne particles. These fine particles, if not effectively collected, settle on equipment surfaces, increasing cleaning frequency and compromising the performance of precision machinery.
An efficient dust extractor machine plays a preventative role by capturing this particulate at the source. It not only safeguards the tableting machine from excessive wear but also ensures that production zones meet GMP and cleanroom standards. Continuous dust extraction leads to better yields and reduced product loss, both of which contribute to measurable operational gains.
Core Components of a Pharmaceutical Dust Extraction System
A complete dust extraction setup typically includes multiple interdependent components engineered to maintain airflow, containment and collection:
- Dust Extractor Unit: The heart of the system, often positioned close to the compression zone to draw in dust directly.
- High-Grade Filter Bags: Typically made from high-viscose materials, these trap fine particles before the air is exhausted or recirculated.
- Dynamic Blower Fan: Designed for low vibration and high-efficiency suction, maintaining steady negative pressure.
- SS 304 Contact Parts: Durable, corrosion-resistant components used in manifolds and trays; SS 316 optional for highly reactive compounds.
- Castor Wheels for Mobility: Allow the dust extractor machine to be relocated easily between different production lines or machines.
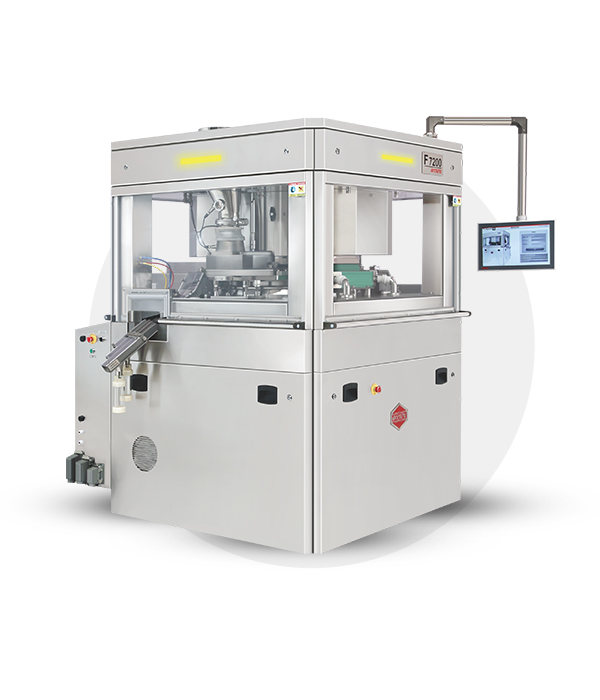
By combining these components, the system ensures optimal dust control without interrupting the tablet manufacturing process.
Operational Advantages of Dust Extraction Technology
The benefits of installing a dedicated dust extraction machine in tablet manufacturing environments go beyond basic cleanliness:
Protecting the Tablet Press
Dust particles can lead to mechanical strain, resulting in punch wear, turret damage and frequent breakdowns. Continuous extraction reduces residue buildup on moving parts, extending the service life of equipment.
Minimizing Cross-Contamination
Uncontrolled dust is a primary source of cross-contamination. A well-designed extraction machine captures airborne powder before it migrates to adjacent equipment or areas.
Enhancing Compliance
Regulatory agencies require documented controls for cross-contamination and airborne particulates. Integrating dust extraction technology supports validation and inspection readiness.
Improving Worker Safety
Inhalable dust poses occupational health risks. By using an efficient dust extractor, the working environment becomes safer and more comfortable for operators.
Features That Improve Efficiency and Reliability
Today's extraction units incorporate several technical upgrades that streamline operations and enhance performance:
- Dual Inlet Manifolds: Allow connection to both a tablet press and a de-burring unit, maximizing coverage without needing separate extractors.
- Stainless Steel Dust Collection Trays: Easy to clean and resistant to corrosion.
- Manual Filter Shaking System: Helps dislodge accumulated powder from filter bags, maintaining optimal airflow and suction levels.
- Noise and Vibration Control: Dynamically balanced blowers ensure quiet, stable operation even during extended use.
These features align with pharmaceutical manufacturing requirements for process control, repeatability and minimal manual intervention.
Choosing the Right Dust Extractor for Pharmaceutical Operations
When selecting a dust extractor manufacturer, decision-makers should evaluate several operational factors:
- Airflow Capacity: Must align with the dust output of the tablet press and de-burring equipment.
- Filter Efficiency: Should effectively trap particles down to micron levels to meet cleanroom standards.
- Ease of Maintenance: Look for systems that offer easy access to filters and trays for cleaning or replacement.
- Integration Capability: Must connect seamlessly with existing tablet compression lines and allow control through central HMI panels if needed.
Working with a supplier experienced in pharmaceutical applications ensures that the chosen system meets operational, compliance and safety expectations.