Tablet compression is a critical process in pharmaceutical and nutraceutical manufacturing, ensuring consistent tablet size, weight and integrity. Among the various tablet press machines, the single rotary tablet press stands out for its efficiency in small to medium-scale production. One of the most important aspects of its operation is the compression force - the pressure applied by punches to compress powder or granules into tablets.
This article explores the role of compression force in single rotary tablet press operations, its impact on tablet quality and best practices for optimizing it.
What is a Single Rotary Tablet Press Machine?
A single rotary tablet press machine is a versatile and compact device designed for compressing powder into tablets in industries such as pharmaceuticals, nutraceuticals and food production. This machine operates using a rotating turret that holds dies and punches. The turret rotates to bring the die under the punches, where compression force is applied to form the tablet.
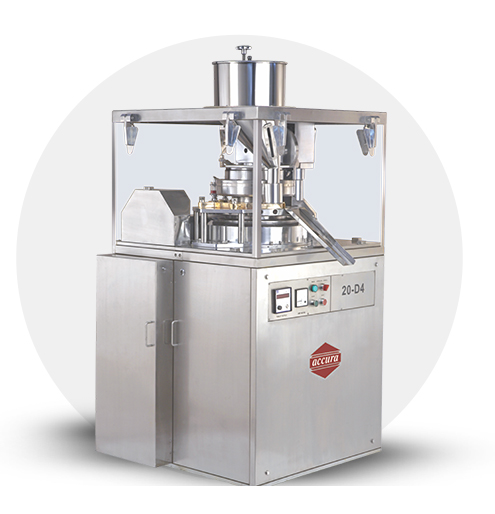
Key Features:
- Bi-layer capability: Allows for the production of multi-layer tablets.
- Adjustable compression and pre-compression settings: Offers flexibility for various tablet formulations.
- Compact design: Ideal for small-batch production.
- Durable construction: Manufactured with stainless steel for corrosion resistance.
The Role of Compression Force in Single Rotary Tablet Press Operations
Compression force refers to the pressure exerted by the upper and lower punches on the material in the die cavity to form a tablet. It is a critical parameter in single rotary tablet press operations, affecting the following aspects:
- Tablet Hardness and Strength
- Compression force determines the hardness of the tablet.
- Insufficient force results in soft, brittle tablets that may crumble during packaging or handling.
- Excessive force can cause capping or lamination, where the tablet layers separate.
- Tablet Weight Uniformity
- Properly adjusted compression force ensures consistent weight across all tablets.
- Uneven force application can lead to weight variations, which affect dosage accuracy.
- Dissolution and Disintegration
- Compression force impacts how quickly a tablet dissolves or disintegrates in the body.
- Higher force produces denser tablets with slower disintegration, while lower force may lead to quicker dissolution.
- Appearance and Shape
- Tablets require uniform pressure to achieve consistent shape and surface finish.
- Improper force can result in chipped edges, uneven surfaces or broken tablets.
How Compression Force Works in a Single Rotary Tablet Press Operation?
The compression process in a single rotary tablet press consists of the following stages:
- Filling: The powder or granules are fed into the die cavity from the hopper.
- Pre-Compression: Light pressure is applied to remove excess air and prepare the material for final compression.
- Main Compression: The upper and lower punches apply the set compression force to form the tablet.
- Ejection: The lower punch rises to push the finished tablet out of the die cavity.
Adjustable Compression Settings
Modern single rotary tablet presses are equipped with adjustable compression and pre-compression settings. These features allow manufacturers to:
- Customize force based on tablet formulation.
- Maintain product quality across different batches.
- Ensure compatibility with various tablet sizes and shapes.
Factors Affecting Compression Force in Single Rotary Press Machines
Several factors influence how compression force is applied and its effectiveness:
- Formulation Properties
- The material’s flowability, particle size and moisture content affect its compressibility.
- Poorly flowing powders may require higher force to achieve uniform compression.
- Punch and Die Condition
- Worn or damaged punches and dies can lead to uneven force distribution.
- Regular inspection and maintenance of tools are crucial for consistent performance.
- Machine Speed
- Operating the press at higher speeds can affect the specified time.
- Shorter dwell times at high speeds may reduce tablet hardness.
- Tablet Size and Shape
- Larger or more complex tablet designs may require higher force for uniform compression.
- Machines must be adjusted accordingly to accommodate these differences.
Optimizing Compression Force in Single Rotary Tablet Press Machines
To achieve optimal tablet quality and production efficiency, manufacturers must carefully manage compression force. Below are some tips:
- Conduct Preliminary Trials
- Perform test runs to determine the ideal compression force for each formulation.
- Adjust pre-compression and main compression settings based on tablet hardness, disintegration and weight requirements.
- Monitor Compression Force Continuously
- Use machines with Programmable Logic Controller and real-time monitoring systems to track compression force.
- Make adjustments during production to ensure consistency.
- Ensure Proper Material Preparation
- Pre-process powders through blending, granulation or drying to improve flowability and compressibility.
- Use a force feeder instead of a gravity feeder for challenging formulations.
- Avoid Over-Compression
- Excessive force can damage tablets and machine components.
- Set force limits based on the material’s physical properties and desired tablet characteristics.
Advantages of Controlled Compression Force
Maintaining precise compression force in a single rotary tablet press offers several benefits:
- High-Quality Tablets: Ensures uniform hardness, weight and size.
- Reduced Waste: Minimizes rejected tablets due to defects.
- Enhanced Efficiency: Increases production speed while maintaining quality.
Challenges in Managing Compression Force
While compression force is critical to tablet formation, certain challenges may arise:
- Material Variability: Variations in raw material properties can affect compressibility.
- Tooling Wear: Over time, punches and dies may wear out, leading to inconsistent force application.
- Operator Skill: Improper machine settings by inexperienced operators can cause quality issues.
Investing in operator training and advanced machines with automated monitoring can help address these challenges.